Under the Health and Safety at Work etc Act 1974 employers are responsible for ensuring the safety of their employees and others. This responsibility is reinforced by The Confined Spaces Regulations 1997 which apply where there is an identifiable risk of serious injury from work in confined spaces : an enclosed space where there is a risk of death or serious injury from hazardous substances or dangerous conditions (e.g. lack of oxygen). These regulations contain the following key duties:
- avoid entry to confined spaces, e.g. by doing the work from the outside;
- if entry to a confined space is unavoidable, follow a safe system of work; and
- put in place adequate emergency arrangements before the work start
A confined space has one or more of the following characteristics:
- Limited access or egress
- The space contains known or potentially hazardous substances and / or atmospheres
- The space is not intended for continuous working
- Conditions of engulfment or entrapment may exist or develop.
Confined spaces include chambers, tanks (sealed and open-top), vessels, furnaces, ducts, sewers, manholes, pits, flues, excavations, boilers, reactors and ovens. Many fatal accidents have occurred where inadequate precautions were taken before and during the work involving entry into the confined spaces.
If you can't avoid carrying out tasks in confined spaces, you must assess the risks of the particular confined space and plan how you will control those risks. The two main hazards are the potential presence of the toxic or other dangerous substances and the absence of an adequate oxygen. In addition, there may be mechanical hazards (entanglement on agitators), ingress of fluids, the risk of engulfment in a free-flowing solid like grain or sugar and raised temperatures.
The work to be carried out may itself be especially hazardous when done in the confined space, for example, cleaning using solvents or cutting/welding work. Should the person working in the confined space get into difficulties for whatever the reason, getting help in and getting the individual out may prove difficult and dangerous. Stringent preparation, isolation, air testing and other precautions are therefore necessary, and experience shows that the use of a confined space permit to work is essential to confirm that all the appropriate precautions have been taken.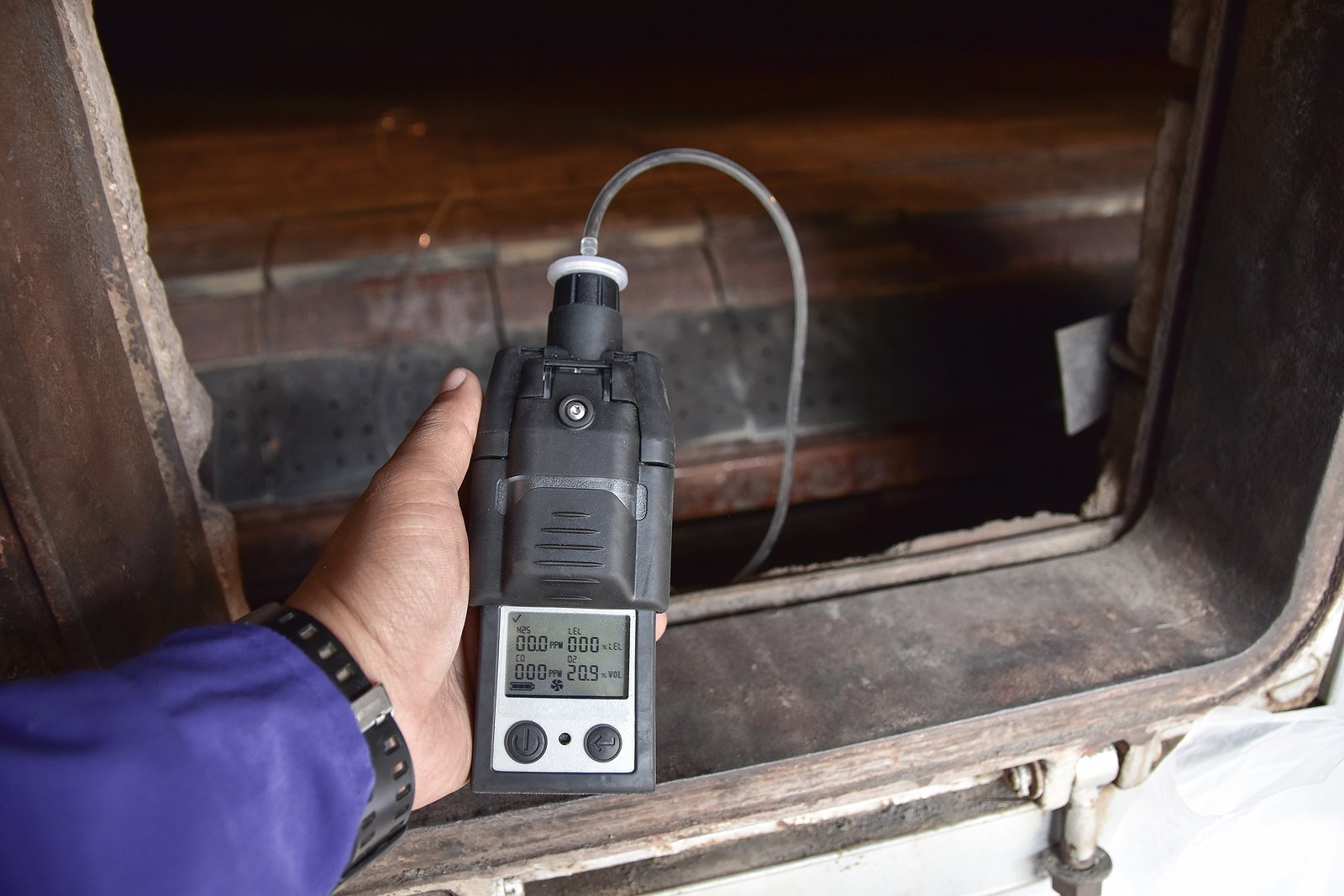
A permit-to-work system is a formal written system and an extension of the safe system of work. A permit is used where there is a reasonably foreseeable risk of serious injury in entering or working in the confined space. The permit to work will form a formal record that all foreseeable hazards and risks have been considered in advance. The precautions required will depend upon the nature of the confined space and the risk assessment, however the main elements to consider are:
- Competence for confined spaces working: ensure all workers are competent, are medically fit and have received adequate training
- Ensuring there is an adequate communication system
- Testing/monitoring the atmosphere: The atmosphere within a confined space must be tested for hazardous gas, fume or vapour prior to entry. Constant monitoring of the atmosphere around the works party is required for the full duration of the job. Records should be kept of the results and findings.
- Gas purging: Where the risk assessment has identified the presence or possible presence of flammable or toxic gases or vapours there may be a need to purge the gas or vapour from the confined space.
- Ventilation: Some confined spaces are enclosed to the extent that they require mechanical ventilation to provide sufficient fresh air to replace the oxygen that is being used up by people working in the space. This can be done by using a blower fan and trunking and/or an exhaust fan or ejector and trunking.
- Isolation from gases, liquids and other flowing materials: Confined spaces will often need to be isolated from ingress of substances that could pose a risk to those working within the space.
- Isolation from mechanical and electrical equipment: power should be disconnected, separated from the equipment, and a check made to ensure isolation has been effective. Check there is no stored energy of any kind left in the system that could activate the equipment inadvertently.
- Personal protective equipment (PPE) and respiratory protective equipment (RPE): So far as reasonably practicable you should ensure that a confined space is safe to work in without the need for personal protective equipment (PPE) and respiratory protective equipment (RPE) which should be a last resort, except for rescue work. Use of PPE and RPE may be identified as necessary in the risk assessment, in which case it needs to be suitable and should be provided and used by those entering and working in confined spaces.
- Gas supply by pipes and hoses: the use of pipes and hoses for conveying oxygen or flammable gases into a confined space should be controlled to minimise the risks.
- Access and egress: a safe way in and out of the confined space must be provided allowing quick, unobstructed and ready to use access.
- Lighting: Adequate and suitable lighting should be provided wherever possible.
- Static electricity: exclude static discharges and all sources of ignition if there is a risk of a flammable or explosive atmosphere in the confined space. All conducting items such as steel and supply hoses should be suitably bonded.
- Emergencies and rescue: The arrangements for the rescue of persons in the event of an emergency, required under regulation 5 of the Confined Spaces Regulations, need to be suitable and sufficient, and where appropriate, there will also be a need for necessary equipment to enable resuscitation procedures to be carried out. The arrangements should be in place before any person enters or works in a confined space.
- Limited working time: there may be a necessity to limit the time period that individuals are allowed to work in a confined space.
The use of a permit system does not, by itself, make the job safe, however, it supports a safe system of working and also provides a ready means of recording findings and authorisations required to proceed with entry.
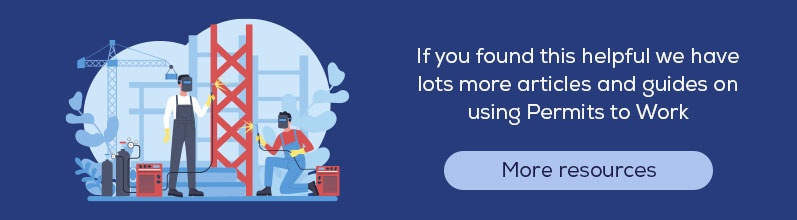